TPM(全名为Total Productive Maintenance,即全员生产维护)是一种强调全员参与、全面参与设备维护的管理方法。通过有效的TPM实践,企业可以优化设备运行,提高设备可用性,降低故障率,从而实现生产效率的新高度。
关键步骤与实践:
1. 培训与教育:
- 为员工提供TPM的相关培训,使其了解TPM的核心理念和实施方法。
- 强调设备维护对生产效率的关键作用,激发员工的积极性。
2. 建立清晰的设备管理计划:
- 制定全面的设备台账,记录设备的基本信息、维护历史和性能参数。
- 建立设备巡检、保养、维修的计划和流程。
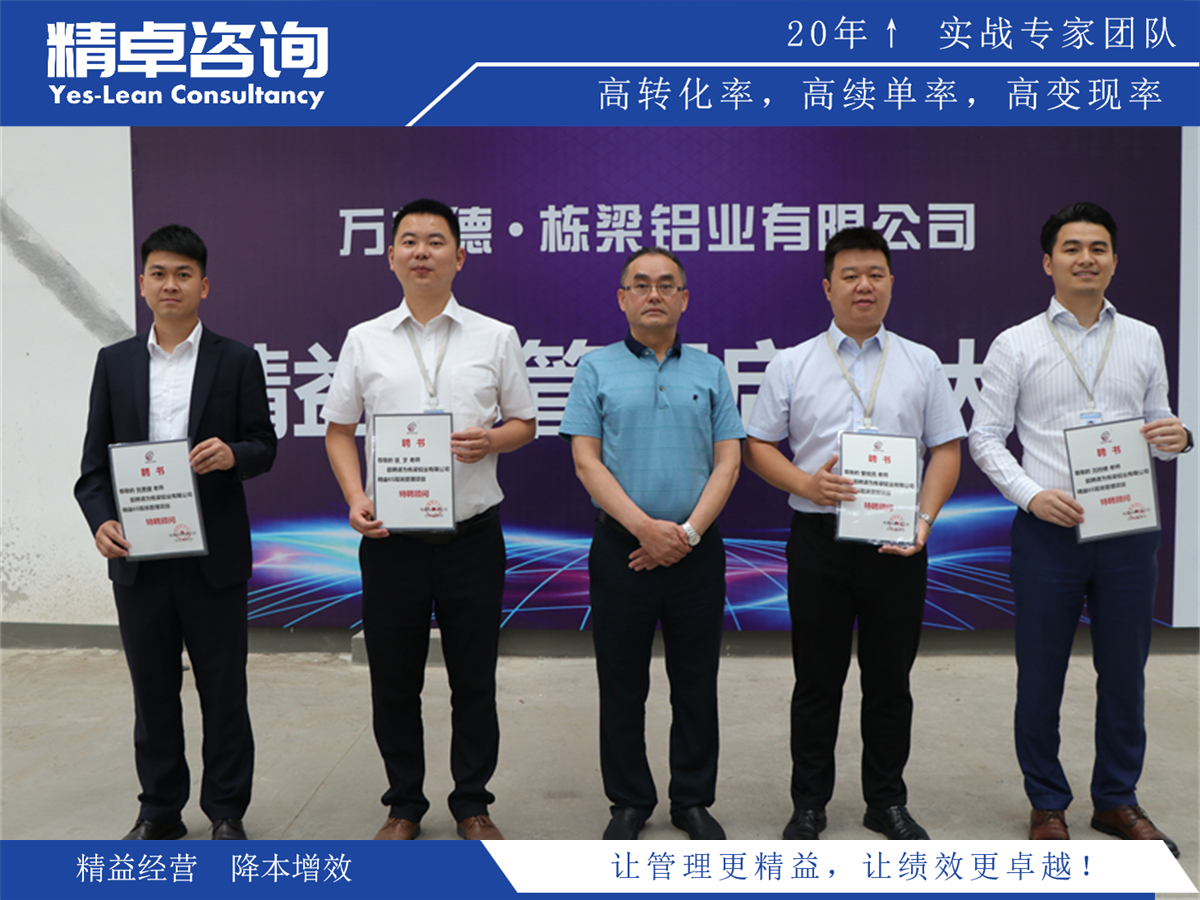
3. 实施计划性保养:
- 制定设备的计划性保养计划,确保设备在规定时间内接受维护。
- 注重预防性维护,降低突发故障的概率。
4. 故障排除与持续改进:
- 建立故障排除机制,迅速响应设备故障,降低停机时间。
- 实施持续改进,分析设备故障根本原因,采取措施防止问题再次发生。
5. 设备效率监控:
- 制定设备效率的监控指标,如OEE(Overall Equipment Effectiveness)。
- 实时监测设备运行状态,及时发现潜在问题。
6. 员工参与与自主性:
- 鼓励员工参与设备维护,培养其自主性。
- 设立奖励机制,激发员工提出改进建议和参与TPM活动。
7. 定期的TPM活动:
- 定期进行TPM小组活动,讨论设备性能、故障情况和改进计划。
- 召开
tpm培训和分享会议,促进经验交流。
8. 标准化工作流程:
- 制定标准的设备维护工作流程,确保操作一致性和标准化。
- 设立清晰的SOP(Standard Operating Procedures),方便员工操作。
优势与成果:
- 设备可用性提升: 通过计划性保养和及时维修,设备的可用性明显提高,降低了停机时间。
- 生产效率提升: TPM的实施有助于提高设备效率和生产率,减少了生产中的浪费。
- 成本降低: 预防性维护降低了紧急维修的成本,全员参与降低了维护的人力成本。
- 持续改进: TPM倡导的持续改进文化有助于推动生产过程不断优化,提高整体管理水平。
通过全面理解和实践TPM,企业能够更好地管理和维护设备,实现生产效率的提升,为持续改进和业务成功奠定基础。