6S管理对制造业不可或缺,目前,国内企业,特别是制造型企业管理混乱,没有章法,急需一套行之有效的管理方法来解决此现状,经过实践得出,6S管理对于企业的管理非常只有效,成为众多企业追捧的管理圣经,今天我们就来谈谈6S管理对于制造业的不可或缺性。
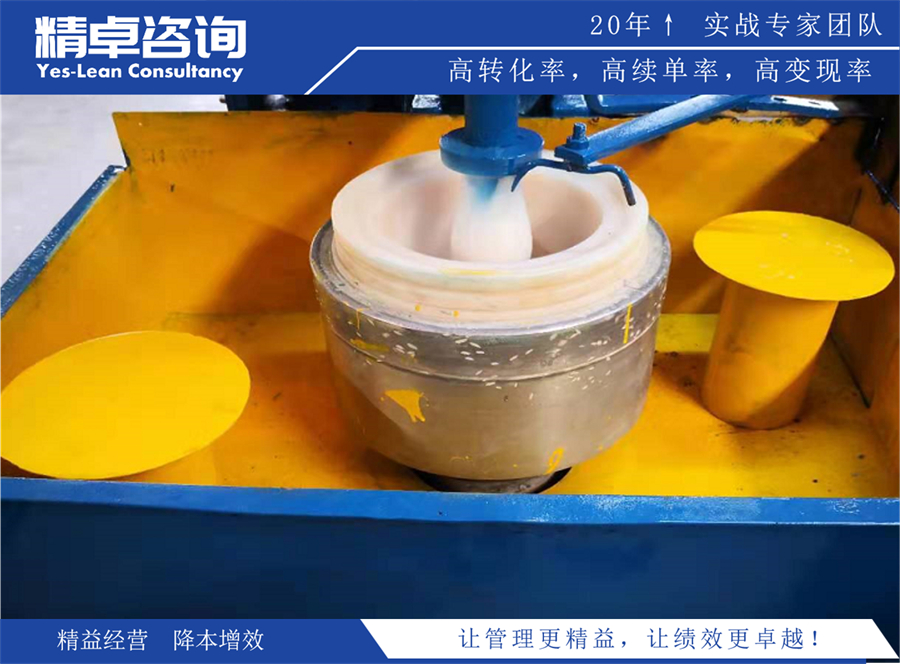
20世纪80年代,一些日本公司在欧美建厂,发现当地人十分反感“个人素养”的说法,于是日本公司的管理者就只提3S或者4S,不提第5个S(素养),所以在欧美企业很少能看到其推行5S。
我曾经在北京给二十多位来自德国的某世界500强公司的中基层管理者培训了一天的精益生产的基础课程《6S及精益现场管理》。在课堂上,德国人多次表示不理解为什么要这么做。问得zui多的是为什么要求在现场、设备设施上画线、涂颜色、贴标识、挂牌?为什么要做这样的改善,按岗位操作手册、作业标准作业不行吗?
这些德国人说:”我们公司从来不做这些改善,我们定期更换设备,定期购入行业内zui好的设备,使用先进的设备、工具来保证效率、质量、安..... 我这才明白这家德国世界500强公司的人为什么不理解精益生产强调的不断改善的思想及6S管理内容,因为该公司的策略是以行业内zui先进的设备、工具来保障效率、质量、安全的方式来满足客户需求,维持自己的竞争力。这也是许多德国公司维持竞争优势的方式, 设备非常先进,自动化程度很高,操作机械设备的工人的专业技能十分出色,做事情严格遵守操作规程。

只是中国有几家企业有资本去实施这种战略,定期投入大量资金购入zui新zui好的设备、机械?此外,就算有钱,管理能不能跟上,员工职业素养是否能达到要求?尤其是人员流动性大的民营企业,如果管理跟不上,难以充分发挥先进设备的作用。如果员工的职业素养跟不上,投入巨资购入先进的机器设备,往往会事倍功半。
对于国内企业来说,现场混乱,制度形同虚设,作业标准可操作性不强,缺乏精细化管理意识,在效率、质量交货、库存等方面与世界一流企业的差距很大是普遍现象。因此,通过6S及精益管理来规范人的作业习惯,提高标准的可操作性,提高作业标准化水平,对优秀作业经验进行总结及推广,通过提高发现问题 与解决问题的能力来弥补某些方面的不足就显得十分重要。这就需要大力推动6S管理,进而推动精益生产。