精益车间
5S管理内容和标准,在现代制造业中,
精益生产是一种重要的生产和组织方法,而5S管理是精益生产中的核心概念之一。5S管理方法旨在改善工作环境,提高生产效率,并减少资源浪费。本文将深入探讨精益车间中的5S管理内容和标准。
第一章:精益车间5S管理体系概述
什么是5S管理?
5S管理是源自日本的管理方法,代表整理(Seiri)、整顿(Seiton)、清扫(Seiso)、清洁(Seiketsu)和素养(Shitsuke)。这五个步骤的目标是创造一个有序、清洁、高效且安全的工作环境。
第二章:精益车间中的5S管理重要性
5S管理对精益车间的影响
精益车间强调消除浪费,而5S管理正是实现这一目标的有效手段。通过优化工作环境,提高生产效率,并减少浪费。
整理(Seiri)
整理步骤涉及评估工作区域,清除不必要的物品,保留必要的物品。这有助于减少混乱,提高工作效率。
整顿(Seiton)
整顿意味着为工具、设备和材料规划明确的存放位置,以便快速访问。这可以减少寻找时间,提高工作效率。
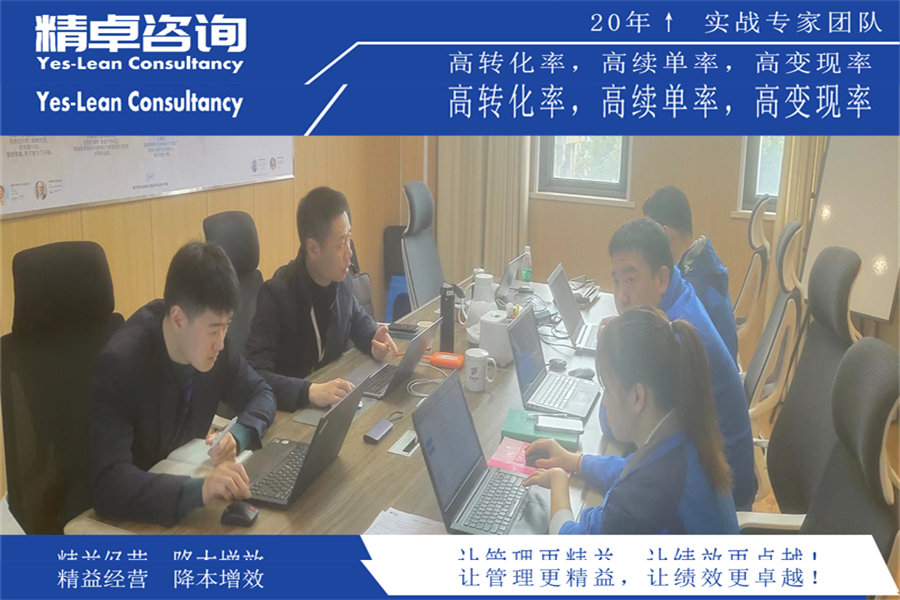
清扫(Seiso)
保持工作区域的清洁和整洁是5S管理的关键组成部分。定期清理有助于创造更安全和舒适的工作环境。
清洁(Seiketsu)
清洁涉及标准化工作区域的清洁程度。通过标识和指示,确保所有人遵循相同的清洁标准。
素养(Shitsuke)
素养阶段强调员工的培训和意识,确保5S标准得到持续遵守。持续的培训和监督有助于保持整洁的工作环境。
第三章:精益车间5S标准化管理的优势
提高生产效率
通过减少搜索时间和资源浪费,5S管理可以显著提高精益车间的生产效率。
减少资源浪费
整理和整顿步骤有助于减少不必要的库存和材料,从而减少资源浪费。
改善质量
保持清洁和整洁的工作区域可以减少错误和缺陷,提高产品和服务的质量。
增强安全性
清扫和整顿步骤可以减少事故和受伤的风险,创造更安全的工作环境。
第四章:实施精益车间5S管理的步骤
评估现状
了解当前精益车间的情况和问题,为5S管理的实施做好准备。
制定计划
制定详细计划,明确实施5S的时间表、责任分工和预期成果。
员工培训
向员工传达5S管理的概念和好处,确保每个人都能理解和支持这种方法。
逐步实施
按照5S的步骤逐步实施,确保每个阶段的平稳过渡。
持续改进
定期评估5S管理的效果,寻找改进的机会并持续优化精益车间的工作环境。
第五章:精益车间5S管理的挑战与解决方案
员工参与度
员工可能对新的管理方法产生抵触情绪,解决方法包括明确好处并提供培训。
维持5S标准
持续维持5S标准需要全体员工的积极参与,可以通过奖励机制激励员工的参与。
企业5S管理中,素养,是对于规定了的事情,大家都按要求去执行,并养成一种习惯达到:让全员遵守规章制度,培养良好素质习惯的人才,铸造团队精神。
在传统的管理中,提高管理水平往往依靠的是设备投入、厂房改进等硬件设施,这种物化的工具和手段,使作业人员只能消极、被动地按照指令进行作业,而用5S管理中素养来提高现场管理水平则完全依靠的是人。
一个企业供应链管理部门的完善与否,不光与硬件实施、仓储条件及员工的专业知识有关,也离不开工作现场精心高效地管理。过去,我们供应链管理部门是依靠GMP来指导工作,员工在某些工作方面缺乏一定主动性和自觉性,比如以前办公室不属于GMP管理范畴,桌面经常会杂乱无章堆积了记账本、台账、书籍等各种东西。
在引进5S管理中,对员工实行分组比较、奖罚制度施,注重员工的个人好习惯的养成及素养的提高,让制度转变成员工的一种习惯。让全体员工养成革除马虎之心、认真对待每一件小事、按规定去完成工作的良好习惯。
结论
在精益车间中实施5S管理是提高效率、减少资源浪费、改善质量和增强安全性的有效途径。通过逐步实施5S方法,精益车间可以创造一个更有序、更清洁且更高效的工作环境。