车间现场5S管理的概述
车间现场5S管理:优化生产现场,提高生产效率,
车间现场5S管理是一种旨在优化生产现场、提高生产效率的管理方法。它借鉴了5S管理的核心理念,结合车间生产环境的特点和需求,旨在建立一个整洁、有序、高效的工作现场。
车间现场5S管理的五个步骤与传统5S管理基本相同,分别是:整理 (Seiri),整顿 (Seiton),清扫 (Seiso),清洁 (Seiketsu),素养 (Shitsuke)。每个步骤都有着具体的目标和操作方法,以帮助车间实现更高的生产效率和质量水平。
车间现场5S管理的五个步骤
以下是车间现场5S管理的五个步骤及其含义:
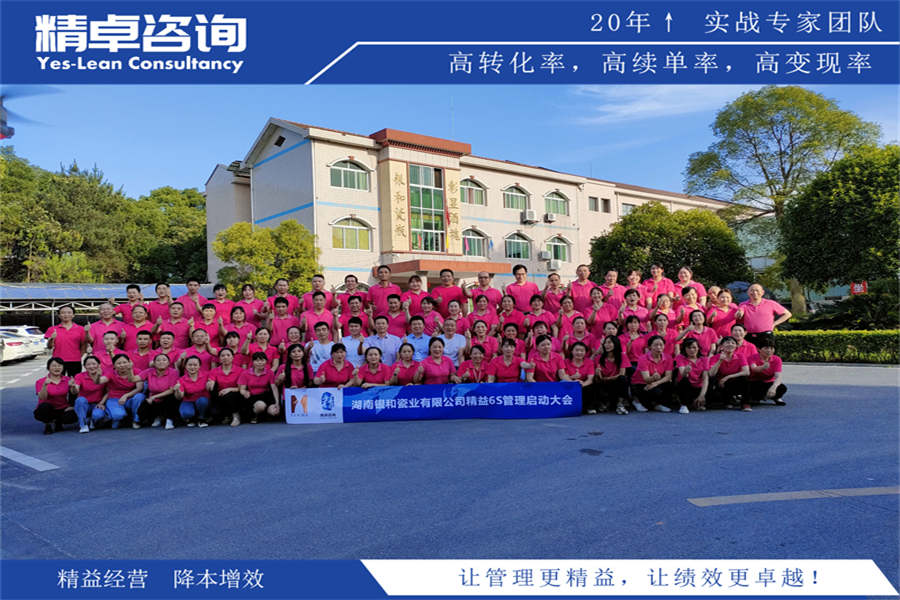
1.整理 (Seiri):整理是指清理车间中不必要的物品,只保留生产过程中必需的物品。通过整理,可以减少车间的杂乱和混乱,提高生产效率。整理的目标是通过分类、标记和分配物品,使车间工作区域更加整洁和有序。
2.整顿 (Seiton):整顿是指对车间进行布局和组织,确保所有物品都有固定的位置和标识。通过整顿,可以减少搜索时间和错误,提高生产效率。整顿的目标是为每个物品分配明确的位置,并确保车间的布局符合生产流程和工作需求。
3.清扫 (Seiso):清扫是指保持车间的清洁和卫生。定期进行清洁和维护可以提供一个舒适和安全的工作环境,减少污染和故障。清扫的目标是保持车间的整洁和干净,并进行日常的清洁和维护工作。
4.清洁 (Seiketsu):清洁是指建立清洁的标准和工作流程。制定清洁的标准和规范,使员工能够理解和遵守清洁的要求。这有助于确保车间的一致性和可持续性。清洁的目标是制定清洁的标准,确保车间的清洁程度符合要求,并建立持续的清洁流程。
5.素养 (Shitsuke):素养是指培养员工的良好习惯和意识,使其能够持续维护整洁有序的工作环境。通过培养素养,员工将自觉地遵守5S管理的原则,并持续改进工作环境。素养的目标是将5S管理作为一种习惯,使其成为组织文化的一部分。
车间现场5S管理的优势和应用
车间现场5S管理具有许多优势和应用场景,包括:
1.提高生产效率:通过整洁有序的车间环境,减少时间的浪费和搜索的困扰,从而提高生产效率。
2.减少故障和事故:通过清洁和维护工作区域,可以减少故障和事故的发生,提高工作安全性。
3.改善工作环境:车间现场5S管理创造了一个整洁、舒适和安全的工作环境,有利于员工的工作积极性和士气。
4.提升质量:通过建立清洁标准和工作流程,可以提高产品和服务的质量,减少错误和缺陷。
5.促进团队合作:车间现场5S管理需要员工之间的合作和协作,可以促进团队的凝聚力和协作能力。
车间现场5S管理方法已被广泛应用于制造业、生产现场、工厂和车间等各个领域,以提高生产效率、质量和员工满意度。
总结
车间现场5S管理是一种优化生产现场、提高生产效率的管理方法。通过整理、整顿、清扫、清洁和素养等五个步骤,可以建立一个整洁、有序和高效的工作现场。车间现场5S管理的优势包括提高生产效率、减少故障、改善工作环境、提升质量和促进团队合作。这种管理方法适用于各种生产环境,是实现持续改进和高效生产的重要工具。